Nous détectons divers modèles de défauts qui peuvent être révélés lors d'étapes de production telles que le fraisage. Ceux-ci incluent, par exemple, les rainures, les pores, les rayures, les défauts et les éclats. Nous utilisons des méthodes modernes telles que la détection d'anomalies pour la détection.
TEST
DES SURFACES INTÉRIEURES
Vérifiez les surfaces internes des surfaces à symétrie de rotation avec notre VISION.SPECTOR.
Notre système de test est spécialement conçu pour examiner les défauts sur les surfaces internes à rotation symétrique pendant la production. De cette façon, vous pouvez vous assurer que les surfaces internes de ces composants sont exemptes de défauts.
Pourquoi les tests en cours de processus dans ces domaines sont-ils si importants ?
Les surfaces internes telles que les carters de turbine, les cylindres de frein, les surfaces intérieures des roulements ou les carters de boîte de vitesses jouent un rôle crucial dans la fiabilité et la fonctionnalité ultérieures de vos composants. Des défauts tels que des rayures, des imperfections, des empreintes d'éclats ou des pores peuvent avoir une influence significative.
Des tests précis en cours de processus de diverses caractéristiques de test sont essentiels pour garantir que vos surfaces à symétrie de rotation répondent aux normes de qualité les plus élevées et garantissent les performances et la sécurité de vos produits.
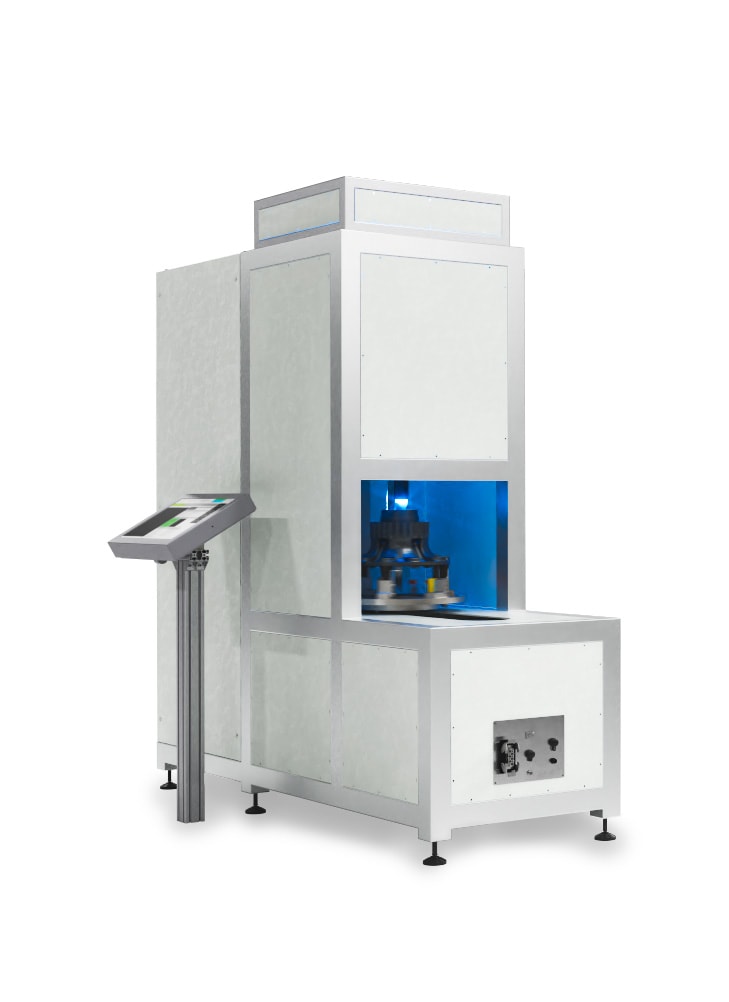
Indispensable pour toute surface à symétrie de rotation
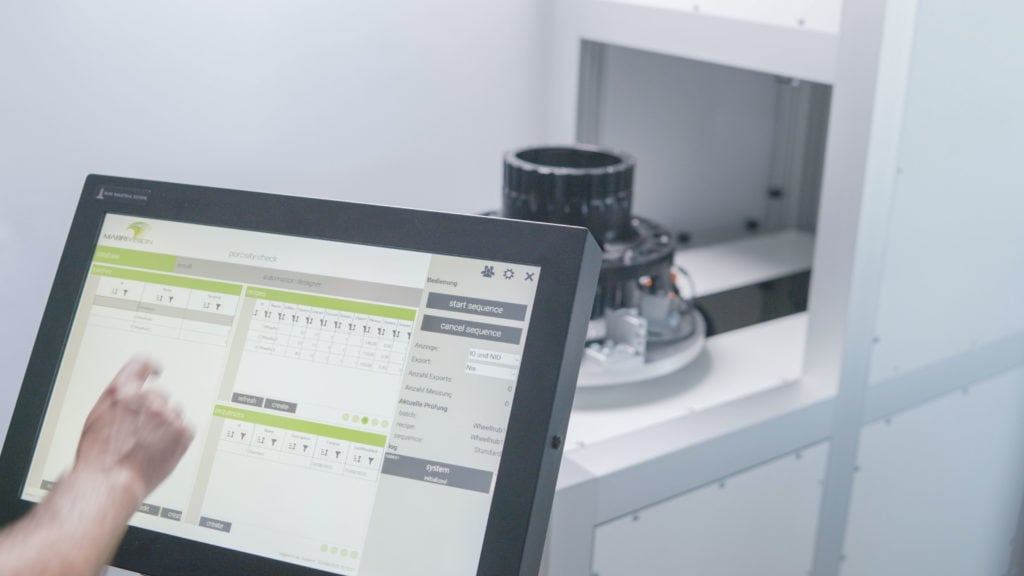
Détection polyvalente des défauts
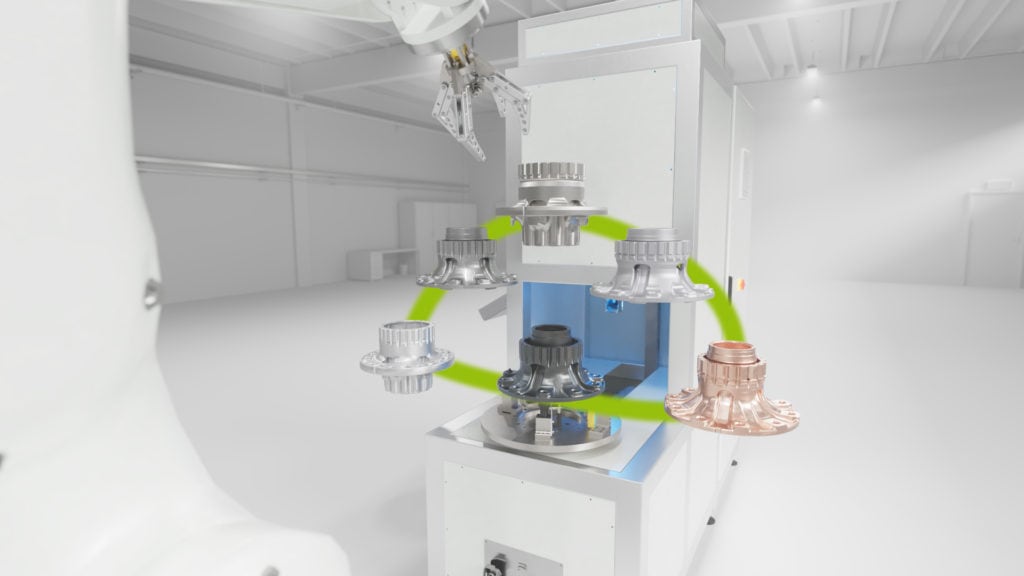
Taille de composant flexible
Grâce à une unité de support flexible, le système de test peut également tester des variantes de composants plus grandes ou plus petites sans avoir à convertir le système. Grâce à la base de données de recettes, la conversion s'effectue en peu de temps.
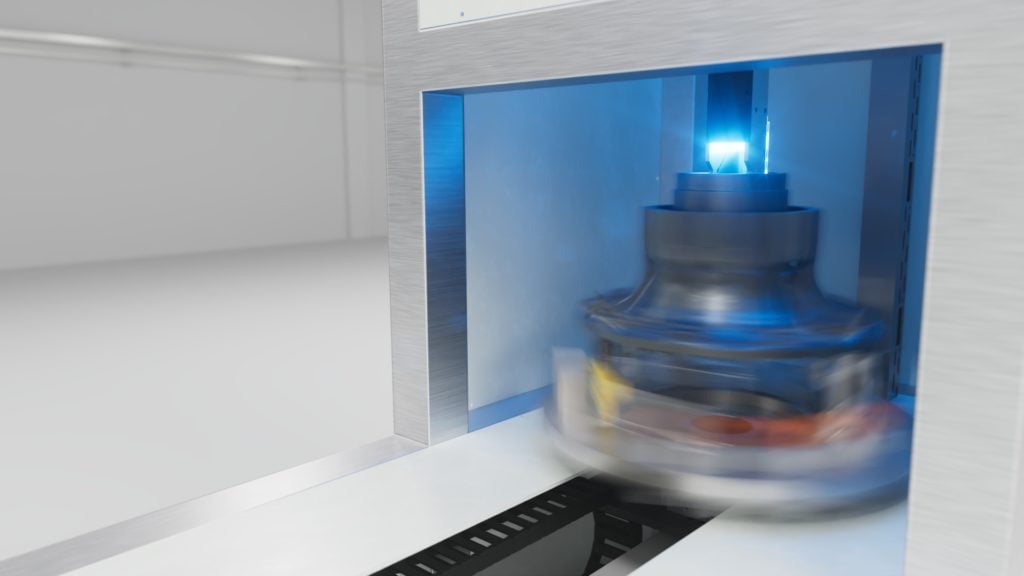
Hautes performances et vitesse
Nous mesurons les pièces d'essai dans des cycles de production avec une vitesse de rotation moyenne de 180°/s. L'axe Z mobile avec une hauteur de mesure mobile de 350 mm permet de tester plusieurs surfaces de diamètres différents en un seul processus.
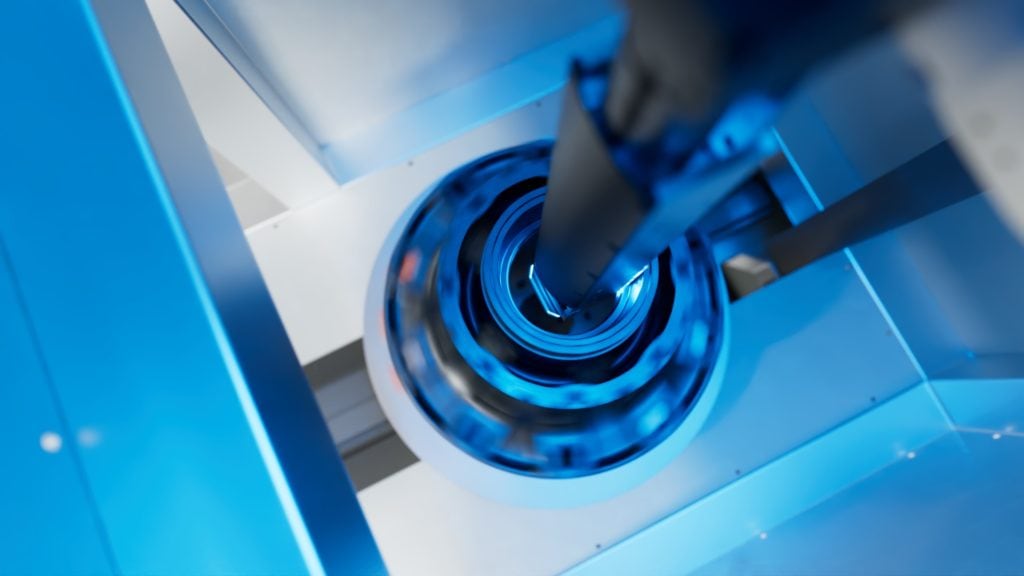
Précision au plus haut niveau
Avec une résolution en pixels d'environ 25 µm, notre système détecte les pores à partir d'une taille de 0,3 mm. Avec un grand champ d'image de 40 mm, nous pouvons couvrir même de grandes surfaces intérieures en quelques secondes seulement.
Exemples d'applications
pour surfaces à symétrie de rotation de divers composants

Test des moyeux de roues
Pour les moyeux de roue, la structure interne joue un rôle clé dans la sécurité de conduite. Des irrégularités ou des défauts peuvent entraîner une défaillance des composants. Des tests approfondis sont donc essentiels.
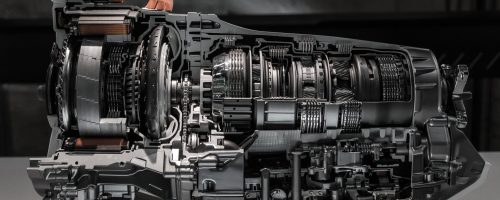
Inspection finale des carters d'engrenages
Les carters de transmission nécessitent de la précision pour une transmission de puissance efficace. Les surfaces internes défectueuses peuvent causer des dommages à long terme et affecter négativement l'efficacité en raison de la traînée de friction.
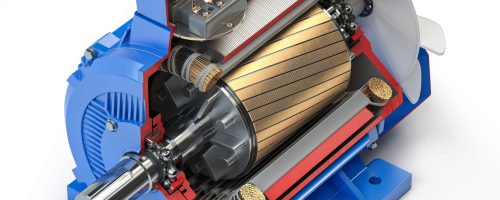
Test des carters de stator
Dans les moteurs électriques, les carters de stator sont essentiels à l’efficacité énergétique et à la longévité. Les défauts ou irrégularités matérielles sont détectés précocement par MABRI.VISION.
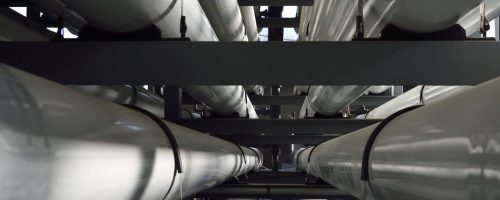
Parois intérieures des appareils sous pression
Ici, l’intégrité et l’étanchéité du conteneur sont de la plus haute importance pour garantir la sécurité et les performances.
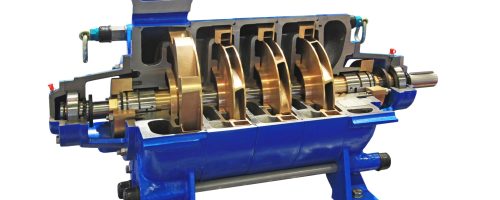
Corps de turbine et de pompe
Les tolérances et les surfaces lisses sont essentielles à la circulation des fluides ou de l'air pour garantir performances, longévité et efficacité.
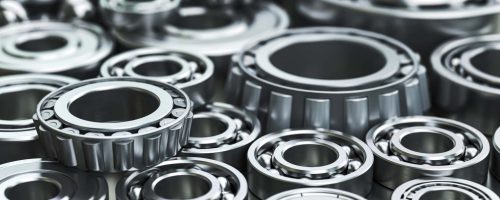
Contrôle final des alésages de roulements
Un perçage précis des roulements est essentiel pour les machines ou les véhicules afin de minimiser les vibrations et l'usure.
La précision rencontre l’innovation.
Découvrez comment nos systèmes de test de vision industrielle font la différence. Parlez à un expert!
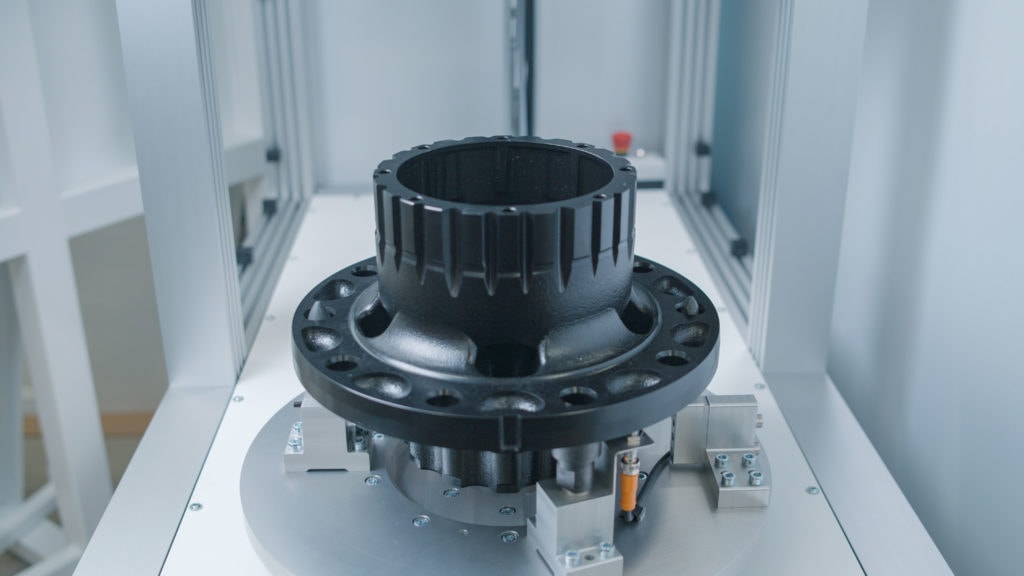
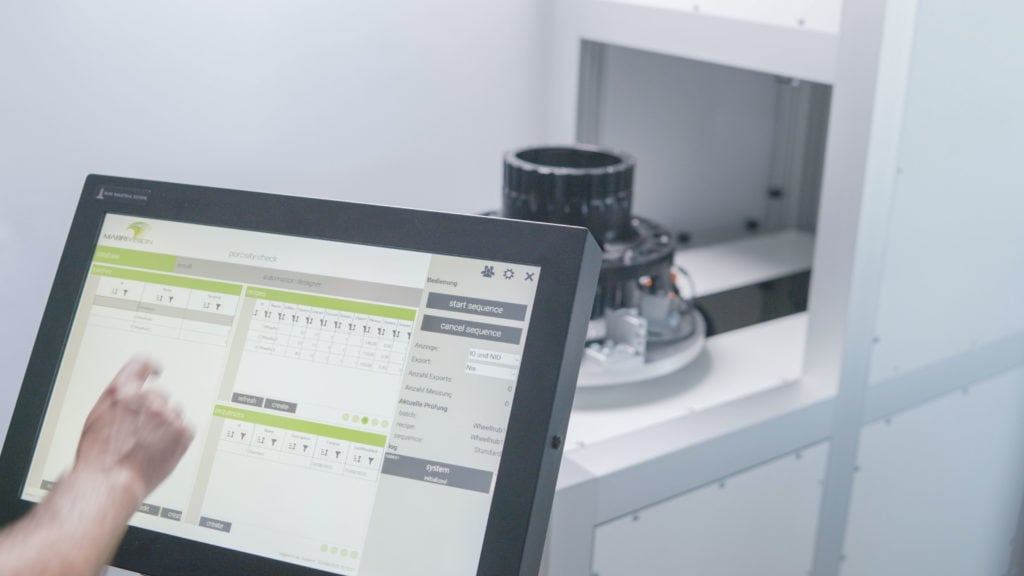
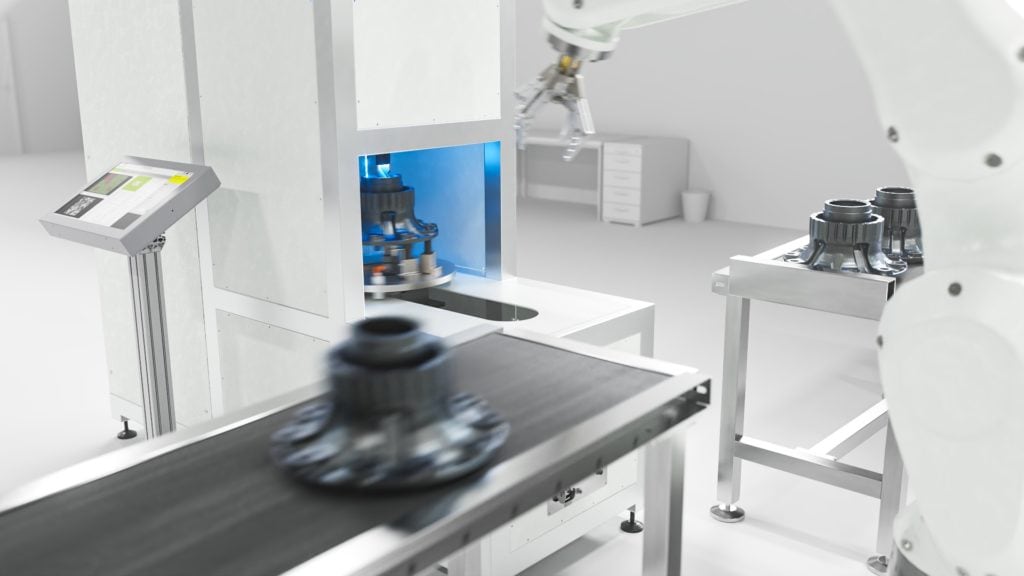
FAQ
Le diamètre minimum que nous pouvons actuellement plonger et tester est compris entre 95 mm et 148 mm. Quant au diamètre maximum, il n’est pas explicitement défini. Dans de tels cas, nous utiliserions l'axe d'alimentation pour positionner les optiques afin qu'elles s'adaptent de manière optimale au diamètre à contrôler. Il est à noter que le champ de vision de l'optique est d'environ 40 mm. Cela permet une adaptation flexible à différentes plages de diamètres dans les valeurs minimales et maximales mentionnées.
Nous pouvons numériser jusqu'à 350 mm dans la plage z. Cela vient du fait que l'axe Z a une portée de 400 mm, même si nous devons déduire un peu d'espace pour la sécurité contre les collisions et la construction de l'optique. Cela laisse une hauteur de mesure effective d'environ 350 mm pour notre numérisation dans la plage Z.
Le temps nécessaire pour retirer un composant Wheelhub du support après l'avoir scanné une fois à 360 degrés est généralement inférieur à 45 secondes. Cette période est composée de différentes étapes du processus. Nous faisons pivoter le composant à une vitesse de 180 degrés par seconde et capturons une rotation complète. La nouvelle position Z est ensuite approchée pour la mesure suivante. Ce cycle dure environ 4 secondes au total. Cependant, la durée totale dépend du nombre de surfaces de mesure qui doivent être numérisées.
Les plus petits défauts que nous souhaitons détecter sont supérieurs à 0,3 mm. Notre résolution en pixels sur la pièce est d'environ 25 µm, ce qui signifie que nous sommes capables de capturer et d'identifier avec précision les pores ou les irrégularités de 0,3 mm ou plus.
La résolution en pixels que nous pouvons atteindre dépend fortement de la taille de la zone de mesure. Une règle simple s'applique : plus la zone de mesure est petite, plus la résolution pouvant être atteinte est élevée. Par exemple, avec une zone de mesure de 20 mm, nous pouvons atteindre une résolution d'environ 12,5 µm.
Cependant, pour des résolutions encore plus élevées, nous aurions besoin d’une nouvelle conception optique et éventuellement d’un équipement spécialisé. De grands sauts de résolution nécessitent généralement une réorientation de l'optique et éventuellement un ajustement de l'ensemble de la configuration du système.
L'objectif principal est principalement la détection des pores. Cependant, nous sommes en mesure d'identifier tout écart, notamment les rayures, la décoloration, les imperfections, les corps étrangers et autres défauts. Cette détection se fait par Détection d'Anomalies. Les erreurs potentielles potentielles sont ensuite évaluées et filtrées à l’aide de Halcon. Cela garantit que nous pouvons détecter et tester de manière fiable un large éventail de défauts.